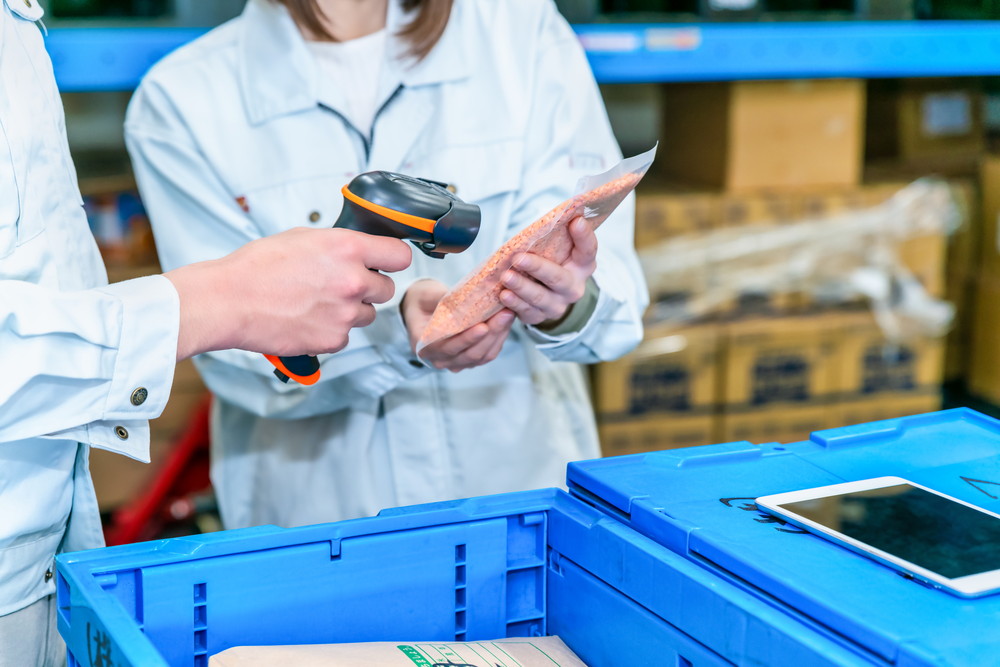
物流現場では、スムーズな出荷作業のためにピッキング作業が重要視されています。
ピッキング作業は顧客へ商品を発送する前工程として重要性が高い反面、ミスの生や、時間がかかりやすい作業の一つです。ミスを避けながら物流業界全体の課題である生産性向上を実現するには仕組みづくりが欠かせません。
しかし、実際にピッキング作業時のミスを防ぐためには、どうすれば良いのでしょうか。
ここでは、ピッキング作業の概要や課題、効率的に作業を行うためのポイントなどをご紹介します。
目次
- 1.
- 2.
- 3.
- 4.
- 5.
- 6.
1.ピッキング作業とは
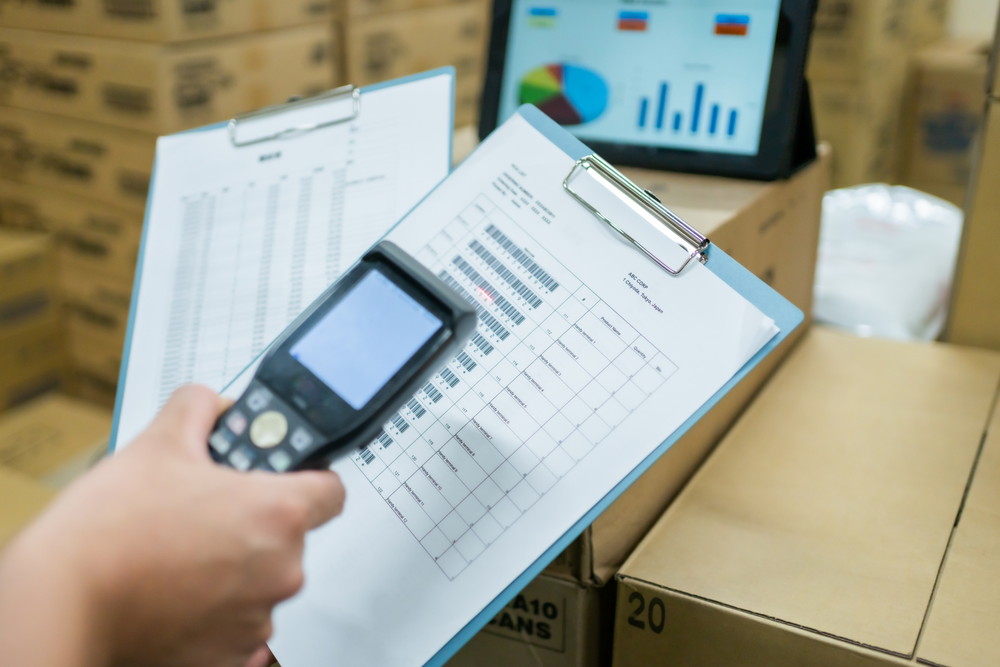
ピッキング作業とは、指示書や伝票(ピッキングリスト)などを基に、倉庫内の商品の中から、出荷指示のあったモノを必要な数だけ集める作業のことです。台車などで商品を集めて、梱包や検品を行う作業者に受け渡すことが基本的な流れになります。
ピッキング作業は、摘み取り式と種まき式の大きく2種類に分けられます。
- 1.摘み取り式
- 2.種まき式
摘み取り式
摘み取り式は、発送先ごとに商品を集めて出荷する方式です。
シングルピッキングやオーダーピッキングと呼ばれる場合もあります。作業内容がシンプルである反面、注文数の増加に伴い、無駄が発生しやすい点がデメリットです。
種まき式
種まき式は、複数の受注の商品をまとめてピッキング作業をしてから、出荷先ごとに仕分けを行う方式です。トータルピッキングやマルチピッキングとも呼ばれます。
一度に複数のピッキング作業を行うことができるため、工数を削減しやすい点がメリットです。ただし、ピッキング作業後の仕分けの工数が多くなりがちである点や、仕分けを行うスペースの確保が必要になる点はデメリットといえます。
2.ピッキング作業の課題
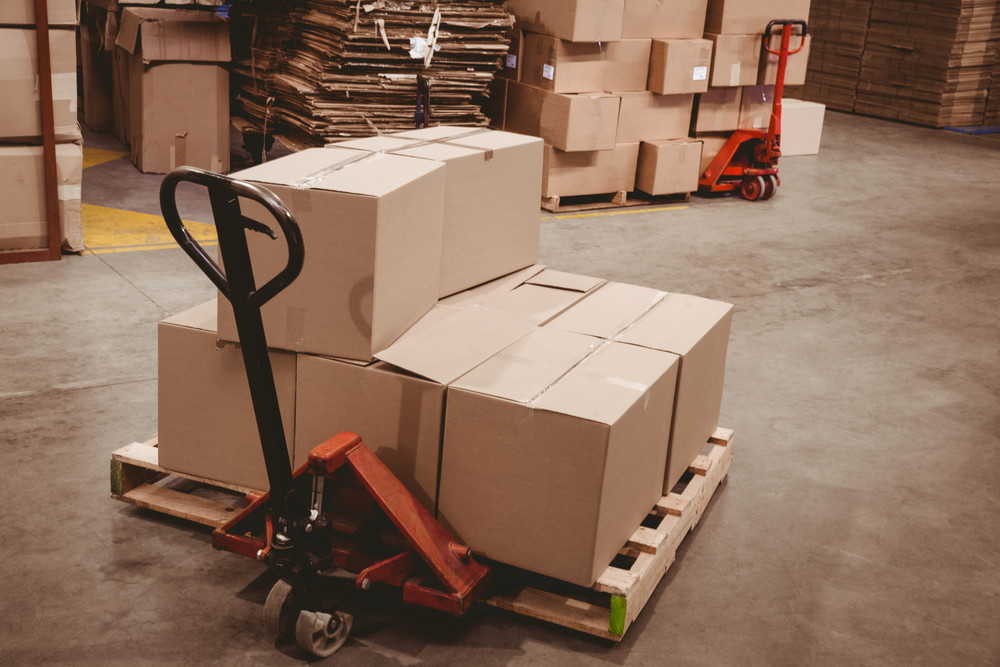
物流業務において、ピッキング作業は課題を抱えやすい作業の一つとして挙げられます。ピッキング作業における主な課題は、以下の2点です。
- 商品の取り間違いが起きやすい
- 商品を探すのに時間がかかる
商品の取り間違いが起きやすい
ピッキング作業時に起こりやすいミスの一つが取り間違いです。
紙の指示書を使った目視点検によるピッキング作業の場合、品番の読み間違いや類似商品との混同、商品の漏れ、数量間違いといったヒューマンエラーが発生する恐れもあります。手作業による在庫管理は在庫情報の正確な記録が難しく、取り間違いや数量間違いといったミスが原因で、在庫切れなどにつながることも考えられます。
商品を探すのに時間がかかる
倉庫が広い、商品配置が分かりにくい、リストの内容が不十分といった問題があると、作業者の移動そのものに時間がかかり、作業効率の悪化につながる点もピッキング作業の課題です。
通路が狭く商品を載せる台車がすれ違えないと、商品を探すのに余計な時間がかかる可能性があります。また、人が作業を行うため、作業効率や精度が作業者の習熟度によって差があるのも課題の一つです。
3.ピッキング作業の課題を解決する方法
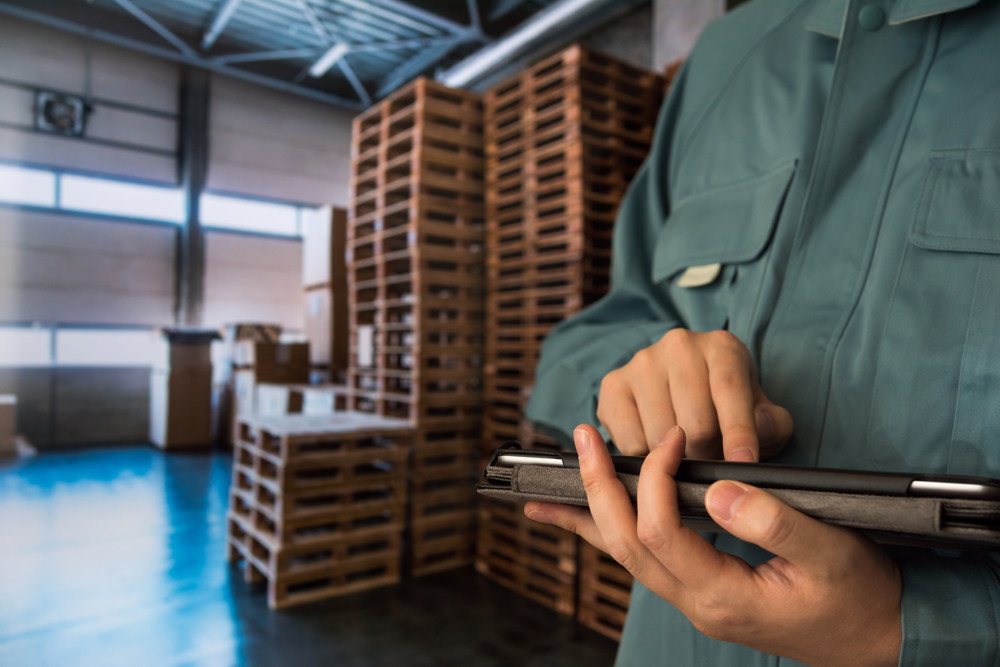
ピッキング作業時の課題を解決するために、以下の4つの方法が考えられます。
- ロケーションの見直し
- ルールの作成
- ピッキングリストの見直し
- システムの活用
ロケーションの見直し
ピッキング作業の課題を解決する方法として、ロケーションの見直しが挙げられます。倉庫内の商品配置を見直したり、棚に番号を振ったりして、どこに何があるのかを把握しやすくすれば、ミスの削減や業務の効率化につなげられるでしょう。
類似商品は距離をあける、取り出す頻度が高い商品は手前に置くといった方法も、ピッキング作業時のミスの減少や、作業の効率化につながります。
また、棚同士の間隔など、倉庫内のレイアウトを再検討することも重要です。作業者の移動距離を減らすことにつながり、作業時間の短縮が見込めます。
ルールの作成
ピッキング作業時のルールや手順を作成し、作業者に徹底させることもピッキング作業の課題を解決するために重要です。マニュアルを作成して、それに応じた作業を実施してもらうことで、作業者による作業品質の差をなくすことにつながります。
また、一度作ったルールをそのままにするのではなく、商品の変化に応じて見直すと良いでしょう。商品の確認ミスを防ぐために、ダブルチェックを徹底することも効果的です。
ピッキングリストの見直し
ピッキング作業の課題を解決する方法の一つが、ピッキングリストの見直しです。
ピッキングミスが起こる要因として、ピッキングリストが分かりにくいことが考えられます。ピッキングリストに不要な情報が載っていると、作業者が情報を取り間違える可能性が高くなります。
品番や数量、ロケーション以外の不要な情報の記載は避け、シンプルなリストの作成を心掛けましょう。また、重要な情報は文字を大きくしたり、色を付けたりするなど、可読性を高める工夫も大切です。
システムの活用
ピッキング作業を効率的に行うために、システムを活用することもおすすめです。
例えば、棚に設置された表示器の指示に従って商品をピッキングする「デジタルピッキング」なら、作業者の習熟度に関わらず一定の作業品質が保証されます。
また、RFIDの活用によって、目視でリストと商品を見比べる必要がなくなるため、商品を取り間違えるリスクを削減することも可能です。
在庫管理システムとデータを連携させて、在庫情報をリアルタイムに更新できる点も、システムを活用するメリットといえます。ピッキングシステムの導入によって、ピッキング作業のミスが減り、効率的に作業が進められるようになるでしょう。
4.ピッキング作業の効率化にはサトーのVoiSolと経路案内ソリューションがおすすめ
ピッキング作業の効率化には、サトーの「VoiSol Smart」や「Visual Warehouse」を活用するのがおすすめです。
VoiSol Smartはウェアラブルデバイスで、音声ガイダンスを提供するシステムです。この音声ガイダンスに従ってピッキングする商品がある棚へ移動することで作業の効率化が実現できます。
また、複数伝票を同時にピッキングしたり、注文内容にあわせて伝票の振り分けを最適化できます。作業も音声ガイダンスに従うだけなので、作業者の習熟度によって作業精度が左右されにくい点もメリットです。
システム開発不要のパッケージ商品なので、現在使用中のシステムとも容易に連携できます。
RFIDを導入する場合は、事前に対象となる現場環境を確認し適切なタグを選定の上、使用環境で読み取りテストを実施することをおすすめします。
経路案内ソリューション「Visual Warehouse」とは、最短経路アルゴリズムと作業者誘導法により、経験値に依存しない生産性を研修不要で実現する倉庫作業者支援ツールです。独自のアルゴリズムを用いて現在地からの最短経路を算出し、最適な順序と経路を指示するので、ピッキング作業にかかる時間の短縮につながります。
カーナビのような分かりやすい画面と音声ガイダンスにより、経験の浅い作業者でも、まるで熟練者のように作業を行うことが可能です。
5.サトーのピッキングシステムの導入事例
ここからは、サトーの経路案内ソリューションを導入した事例をご紹介します。ピッキング作業の課題を解決するヒントになれば何よりです。
佐川グローバルロジスティクス株式会社様 事例
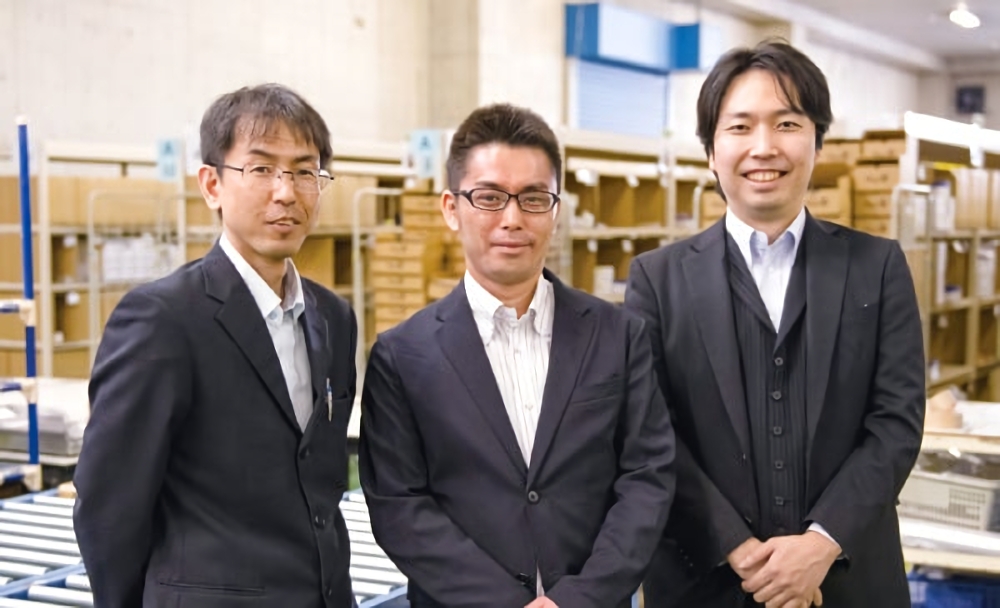
近年は、需要の増加や少子高齢化の影響もあり、物流業界全体で人材確保に苦慮しています。そのような中、クライアントのバリューチェーンを物流からサポートする佐川グローバルロジスティクス株式会社様では、新規クライアントとの契約が決まり、ピッキング作業の効率化が求められていました。
そこで同社は、最短経路ナビゲーションシステムを搭載するサトーの倉庫内経路案内ソリューション「Visual Warehouse」を導入し、ピッキング作業の大幅な効率化を実現しています。
【導入前の課題】
- 人員不足を補うために、既存作業者の生産性向上が急務
- 多品種のピッキング作業における倉庫内の移動距離、時間の大幅な増加
- 作業者による生産性の差や、育成にかかる負担の増加
【導入による効果】
- 導入1カ月後に生産性が23%向上
- 倉庫内の適切な経路ナビゲーションにより移動距離と時間が半減
- 研修不要で全ての作業者が熟練者同様のパフォーマンスを実現
具体的な事例内容については、以下もご覧ください。
6.ピッキング作業の効率化は作業環境がカギ
手作業によるピッキングは、ミスが発生しやすく作業者ごとに正確性やスピードが左右されやすい点も課題といえます。業務効率化のためには、作業環境を改善することが重要です。
作業環境の改善にピッキングシステムを導入すれば、ミスの削減に加えて業務の効率化も期待できます。ピッキング作業でお悩みの場合は、システムの導入を検討してみてはいかがでしょうか。
ピッキングシステムの導入を検討する際には、ぜひサトーまでお気軽にご相談ください。
- テーマ:
- 音声認識