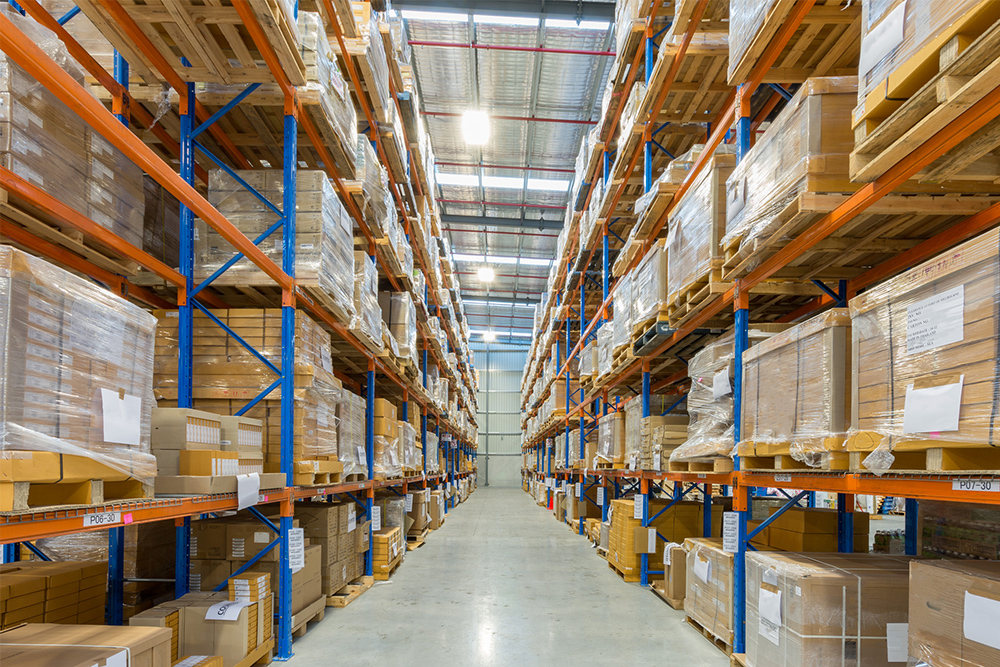
工場や倉庫といった現場では、常に多くのモノやヒトが動き続けています。それらの管理をバーコードや手書きといった人手で管理していると、煩雑さによる問題が発生しかねません。
問題を解決する方法の一つに、システムの活用が挙げられます。例えば、位置情報を把握できるシステムを導入すれば、簡単にモノやヒトの所在管理を行えるようになります。
ここでは、モノやヒトの場所を管理する「所在管理」の課題や解決策、サトーの位置測位システムを導入した企業の事例などをご紹介します。
目次
- 1.
- 2.
- 3.
- 4.
- 5.
1.所在管理における現場の課題
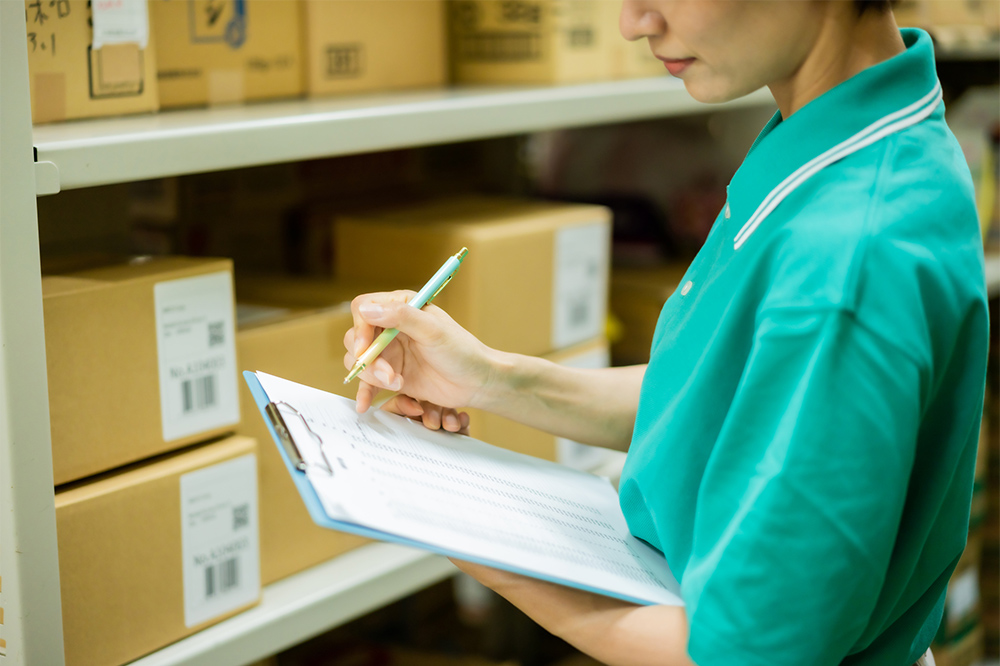
現場の所在管理では具体的にどのような課題があるのでしょうか。
ここでは、工場や倉庫などの現場での課題をご紹介します。
モノの位置が分からない
工場や倉庫などは、部品や資材、運搬に必要な備品など多くのモノで溢れています。それらの在庫数や持ち出しの履歴、置き場所(ロケーション)などがデータ化されていないと、モノの位置が分からなくなり、「いつ、どこに、何が、どれだけ」あるのかを把握できません。
位置が把握できなければ、モノを探すのに時間がかかり業務効率が悪くなる他、追加発注が発生して費用がかさんでしまうことも考えられます。また、法律で廃棄方法が定められている資材などが一般ごみに混入する恐れもあります。
さらに、棚卸し業務の負担が重くなるというデメリットも挙げられます。
ヒトの業務内容を把握しにくい
一般的に工場や倉庫では、各々の業務フローが決まっていてそれぞれが定められた業務を行います。
しかし、「いつ、どこで、誰が、何を、どれだけ」作業しているのかが具体的に分からず作業の進捗状況が把握できないと、人員を適切に配置できません。工程およびコスト管理が難しく、作業効率の低下も課題です。
また、業務内容が把握できないということは問題点も分かりづらく、具体的な業務改善方法の検討には至りません。
作業動線の可視化が難しい
モノやヒトの所在が分からないと、作業動線の無駄に気付けない可能性があります。特定の場所で滞留しやすい、移動に余計な時間がかかるなど、動線の無駄は大きな課題です。
しかし、作業動線の把握には、一つ一つの作業状況を動画で撮影し記録や分析を行うなど、非常に手間がかかります。そのため、課題があることは分かっていても問題を先送りにしてしまっている企業は少なくないでしょう。
2.効率的に所在管理をする方法
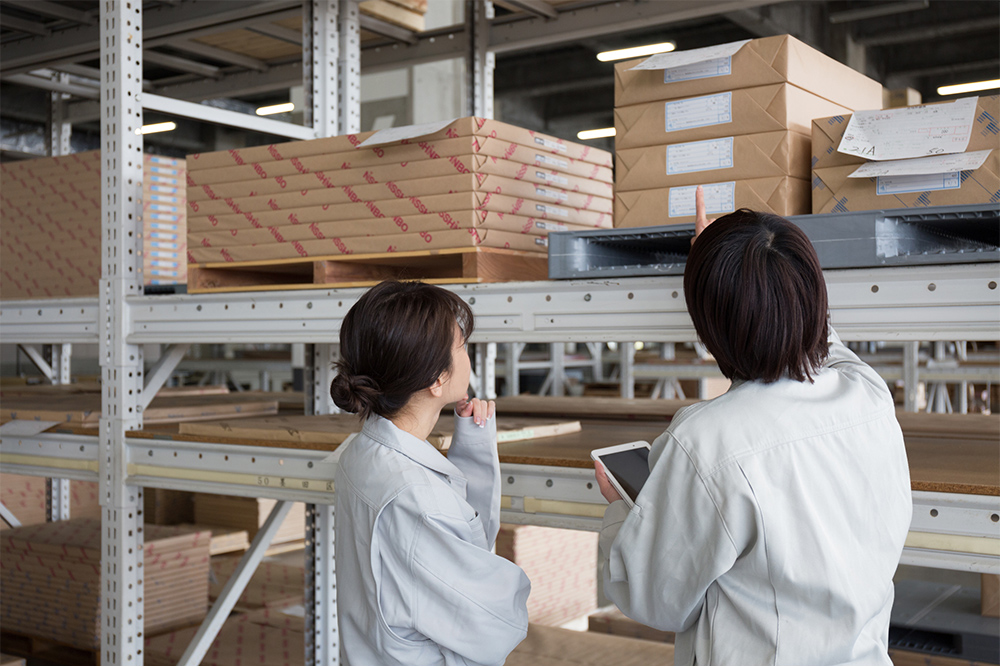
効率的に所在管理をするためには、モノやヒトの位置を把握し動線の無駄をなくす必要があります。ここでは、そのための方法を2つご紹介します。
基本的なルールの徹底・共有
動線の無駄をなくし所在管理を効率化するには、モノの保管場所の管理や先入れ先出しの徹底など基本的なルールの徹底が重要です。
モノの保管場所や方法、持ち出し時のルールなどを徹底することでどこに何があるのかを把握しやすくなり紛失を防げる可能性が高くなります。
また、既にルールを徹底できていても作業員への共有がうまくできていないという課題を抱えている場合もあります。このような場合には、ルールをマニュアル化したうえで全作業員に共有することが必要です。
システムの活用
システムを活用して所在管理を実施する方法もおすすめです。モノやヒトに専用のタグを取り付けセンサーで自動取得できる環境を整えれば、どこに何があるのかを常に把握できます。
手書きや目視でモノを管理する方法に比べて作業時間が削減でき、精度も向上します。
3.モノやヒトの所在管理に役立つ「位置測位システム(RTLS)」
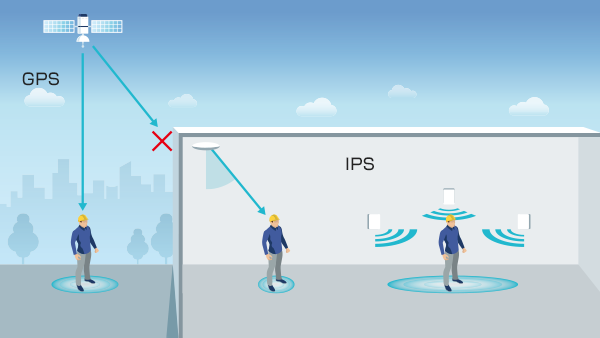
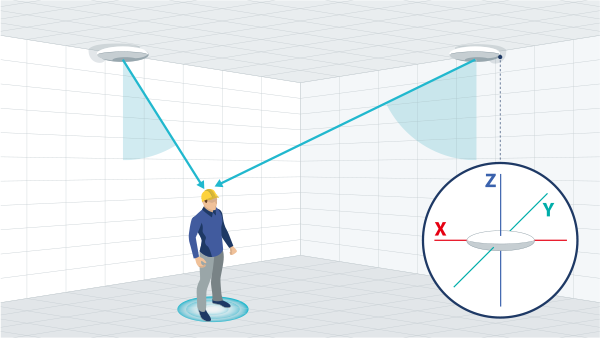
サトーではモノやヒトの所在管理に役立てられる、3つの「位置測位システム(RTLS:Real Time Location System)」を活用したシステムを提供しています。
- UbisenseUWB
- Quuppa
- EXBeacon
位置測位システムとは、モノやヒトが「ある時点」で「どこにあるか」を知るために、位置を測定する技術のことです。
ここでは、サトーの位置測位システムの概要と導入メリットについてご紹介します。
サトーが提供する3つの位置測位システム
サトーが提供する3つの位置測位システムは、モノやヒトに専用タグを取り付けたうえで専用の受信機(ロケーター)を使用し、位置を測定する技術です。3種はそれぞれ測位精度や速度に違いがあるため、現場に合うものをお選びください。
「UbisenseUWB」の位置測位精度は、30cm~です。非常に正確な位置情報を測定できます。位置測位したモノを画面に表示するまでのスピードも早く、位置情報をほぼリアルタイムで把握できます。高性能で使い勝手のよい位置測位システムをお求めなのであれば、こちらがおすすめです。
「Quuppa」の位置測位精度は、50cm~です。UbisenseUWBに比べて、位置測位精度と表示スピードは劣りますが、電波干渉に強く電力消費量が少ないなど機器設置の自由度に優れていて、導入コストとのバランスから導入実績が多いです。
「EXBeacon」の位置測位精度は、2、3m~です。3種の中では位置測位精度も表示スピードも大きく落ちますが、最も低コストで導入可能です。また、設置やネットワーク接続などのインフラ構築がしやすく、移設も簡単にできます。
「ヒトがいる・いない程度のことが分かれば十分」「高い精度は必要ない」という現場や、「低コストでフレキシブルに設置したい」といった現場に適しています。
位置測位システムの導入メリット
位置測位システムを活用すれば、ヘルメットや車体などに付いたタグを受信機(ロケーター)で読み取り位置情報を取得することが容易になります。「いつ、どこで、誰が、何を、どれだけ」行っているのか、作業の進捗状況を一目で把握できるようになります。
また、位置測位システムで取得した情報から、作業者と作業実績をひも付けて作業工程を可視化できるため、作業工程や動線の改善、効率的な人員配置などにもつながり現場の改善に役立ちます。
さらには工場や倉庫内で使用する資材にタグを取り付けることで、位置情報を高精度で把握できるようになります。リアルタイムで在庫の所在を確認できるので棚卸し業務が不要になり人的負担やコストの軽減を実現できます。
4.所在管理におけるサトーのシステム導入事例
ここからは、サトーの位置測位システムを導入することによって、所在管理の課題を解決した事例をご紹介します。
位置測位システムで資材の所在を可視化
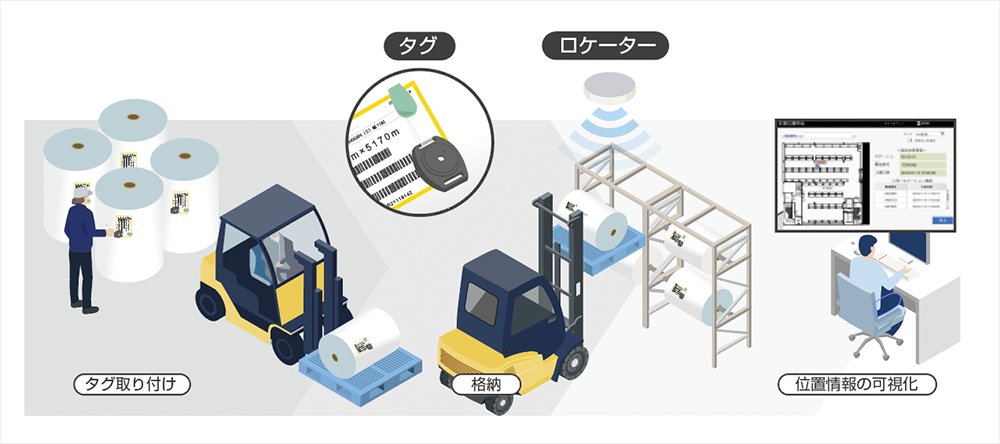
工場や倉庫内に点在する「原反ロール」や「フレキシブルコンテナバッグ(フレコン)」は、重量が数百キロ~1トンを超えるためフリーロケーションで平置きされるケースが一般的です。
重量がある大型製品の位置管理は、現場の一部の熟練作業者に頼る場合が多くモノの位置を全員が容易に把握できないのが現状です。探索の手間や紛失のリスク、トレーサビリティーなどの観点においても所在管理の徹底は急務といえます。
サトーでは位置測位システムを活用することで、資材の所在を可視化し、現場の「探す」無駄ゼロを実現します。
【導入前の課題】
- 大型資材の置き場が分からないため、所在探索に多くの工数が必要
- 台帳記入やExcel入力など手作業による入出庫、在庫管理による人的ミスの発生
- 入出庫履歴を都度確認するため時間がかかる
【導入による効果】
- 位置測位システムの活用により、資材の所在管理と探索が容易に実施可能
- 入出庫・在庫管理をシステム化することで、正確性と業務効率の向上を実現
- 資材の入出庫や所在を可視化することで、作業履歴のトレースが可能
具体的な事例内容については、以下もご確認ください。
5.位置測位システムで所在管理の課題を解決しよう
モノやヒトの位置情報は、在庫数や工程の把握において重要な要素の一つです。位置情報が分からないとどこに何があるのか、どこで誰がどのような作業を行っているのかが把握できず、業務効率の低下を招きかねません。
位置測位システムを活用してモノやヒトの位置を正確に把握し、所在管理における課題を解決することをおすすめします。
モノやヒトの所在管理に課題を感じている場合は、お気軽にサトーまでご相談ください。
- テーマ:
- 位置測位