組立製造現場の課題
人材不足の解消や競争力の強化といった課題に直面している製造業にとって、生産性を向上させ、他社にはまねのできない付加価値の高い製品を生産していくことが重要であることは、言うまでもありません。
一方で、これまでの経験値や現場の判断に依存した作業が常態化していたり、本来なら自動化や外部委託化ができる作業が切り分けられなかったりすることによって、現場にムダな作業が発生しているケースは、まだまだ多いのが現状です。
自動車製造業などの組立製造の現場では、次のような課題に頭を悩ませているという声を聞きます。
1各工程の作業生産性のバラツキが、工場全体の生産性向上の妨げになっている。
組立製造の現場では、工場全体で作業生産性が平準化されていることが重要です。しかし実際には、一部の工程で人手が足りずに生産が滞り、他工程の担当者が本来の持ち場を離れて作業応援するようなケースも見受けられます。このような標準外の作業が増えると、作業効率は下がり、工場全体の生産性が低下する懸念があります。
2“自社にしかできない作業”の比率が低いので、付加価値を上げるための妨げになっている。
工場の組み立てラインでの作業には、“自社にしかできない作業”である直接作業と、例えば「磨き」などのように製造ラインから離れたところで行う間接作業があります。少ない労働量でより多くの付加価値を生み出すためには、直接作業の時間を増やす必要がありますが、実際は間接作業に時間をとられていることがあります。自社の強みを発揮する直接作業に多くの時間を割けないと、生産の付加価値をさらに上げるのが難しくなります。
3工数管理のための作業が発生するため、製造業務に集中できない。
工数情報は生産プロセスに関わる経営判断を下す際に重要です。しかし工数管理のための帳票への記入やデータ入力作業が必要な場合、作業者に負担をかけることとなり、本来注力すべきである製造作業に集中できない事態が発生します。また、工数情報の入力にムラやモレ、ミスがあると、工数情報の信ぴょう性が下がるため、経営データとして活用することが難しくなります。
このような中、IoT技術によって、工場設備の稼働状況や人の作業履歴などのデータを自動で収集し、得られたデータを活用することで、工場の抜本的な品質・生産性の改善を行う、いわゆる「スマートファクトリー」に取り組もうと考える企業も増えてきています。
スマートファクトリー化に向けて、工場でのモノや人の位置情報の活用が注目されていますが、それらは本当に生産性の向上や企業競争力の強化に役立つのでしょうか。
自動車製造業A社様の改善事例
「人やモノの位置情報」から、いつ、誰が、何をどれだけ作業をしているのかを完全把握。現場に負荷を一切かけずに、生産改善に成功。
A社 基本情報
- 業種
- 自動車製造業
- 導入のきっかけ
- 工場を新設するにあたり、さらなる生産性改善を断行。位置測位ソリューションQuuppaを導入した。最新の技術を取り入れた「スマートファクトリー」のグローバルでのモデルケースと位置付けている。
A社の課題
作業者任せの工数管理で、正確な製造原価を把握できていない
A社では決められた作業の開始時と終了時に、専用のバーコードをスキャンし作業内容を入力することで、工数管理をしていました。入力は作業者任せになるため、入力ムラや、入力忘れ、入力ミスが発生していました。正確な工数管理ができないため、製造原価を正確に把握できず、生産性向上のための対策を取るのが難しい状況でした。
工数管理のためのスキャンに手間と時間がかかり、作業時間にロスが発生している
工数情報の入力作業にどれくらいの時間を使っているかを明確にするために、稼働分析を行ったところ、1工程の工数管理に、毎日6,457秒(約108分)かかっていること、また、工数管理の情報をPCに入力するための順番待ちが発生していることが分かりました。
稼働分析をした製造ラインは全15工程で、この工場では12ラインが稼働していました。A社は複数の工場を保有しています。いかに多くの時間を工数管理のために使っていたのかが判明しました。
人材の適正配置や自動化、アウトソーシング対応が後手になっている
工程のどこかで製造が遅れると、他工程の担当者がサポートして、遅れを挽回していました。その際、誰がサポートをするかは、現場の判断で行われていました。マンパワーが不足した際の対応も現場任せとなっており、生産能力を向上させるために人材の適正配置の判断基準が確立されていませんでした。
また、急場をしのぐ配置替えなどの実態把握や、直接作業と間接作業の見える化ができていなかったため、自動化やアウトソースできる作業の切り分けが後手になっていました。
A社でのリアルタイム位置測位導入の3つのメリット
この課題を解決するため、人やモノの位置情報が正確に分かる、サトーの「リアルタイム位置測位」を導入しました。
工数の見える化で、正確なコスト管理が可能に
A地点にいる作業者は、Bという作業をしているというように、位置と作業内容を1対1対応させることで、誰がいつ、何の作業をしているかの把握ができるようになりました。全ての工数が見える化されたことで、正確なコスト管理が可能になりました。
工数管理にかかる時間がゼロで、生産に集中できる環境に
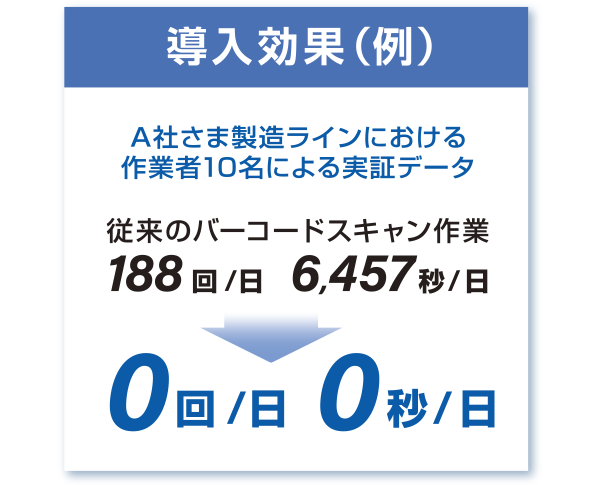
作業者に意識させることなく工数データを取得できるので、工数管理のために作業を中断する必要がなくなりました。以前は1工程に毎日6,457秒(約108分)かかっていた工数データ取得のための作業時間がゼロとなりました。これまで工数管理のために使っていた時間を、本来行うべき生産作業に充てられ、製造に集中できる環境を整えることができました。
人の適正配置で、効率的に生産できる体制に
工数を正確に見える化したことで、付加価値の高いところに人材を集中投下するなど、人の適正配置ができるようになったため、生産性が向上しました。作業内容の実態把握により、直接作業と間接作業を切り分け、間接作業の自動化やアウトソーシングを検討できるようになりました。さらに、工数データの精度が高まったことで、工数管理から得られた情報を経営データとして活用できるようにもなっています。
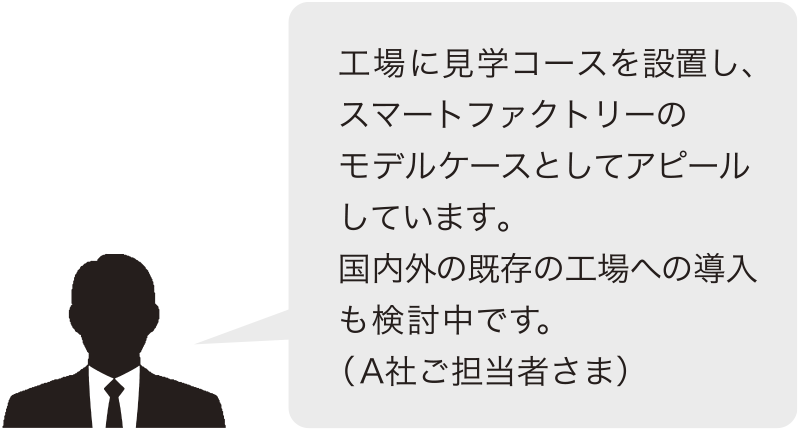
A社様 改善点のまとめ
Before
- 作業者任せの工数管理で、正確な製造原価を把握できていない
- 工数管理のためのスキャンに手間と時間がかかり、作業時間にロスが発生している
- 人材の適正配置や自動化、アウトソーシング対応が後手になっている
After
人やモノの位置情報が正確に分かる、サトーの「リアルタイム位置測位」を導入
- 工数の見える化で、正確なコスト管理が可能に
- 工数管理にかかる時間がゼロで、生産に集中できる環境に
- 人の適正配置で、効率的に生産できる体制に
サトーの位置測位ソリューションQuuppaだからできること
現場に負荷をかけず、自動的に作業工数の集計が可能
Quuppaはロケーター(リーダー)とタグの配置から、誤差50cm~1m程度まで詳細に絞り込んで位置情報を測ることが可能な技術で、製造現場内を正確にセンシングできるソリューションです。 作業者のヘルメットや製造ラインに付けられたタグを読み取り、位置情報から作業内容を特定する仕組みのため、工数データを記録する作業が一切不要です。作業者は、意識することなく通常の作業をするだけで、自動的に作業工数が集計されます。
導入実績が豊富。導入時には徹底的に検証を重ねます
位置測位センサーは電波を使用するため、金属や水が存在する環境では通信に影響が出る可能性があります。電波の干渉もあるため、センサーの設置場所やタグの貼付方法に工夫が必要です。 サトーは、これまでの導入実績を踏まえ、設置場所の環境に配慮した設計を行えます。正しく工数情報を取得できるよう、徹底的に検証を重ねます。位置測位ソリューションの導入は、経験豊富なサトーにお任せください。
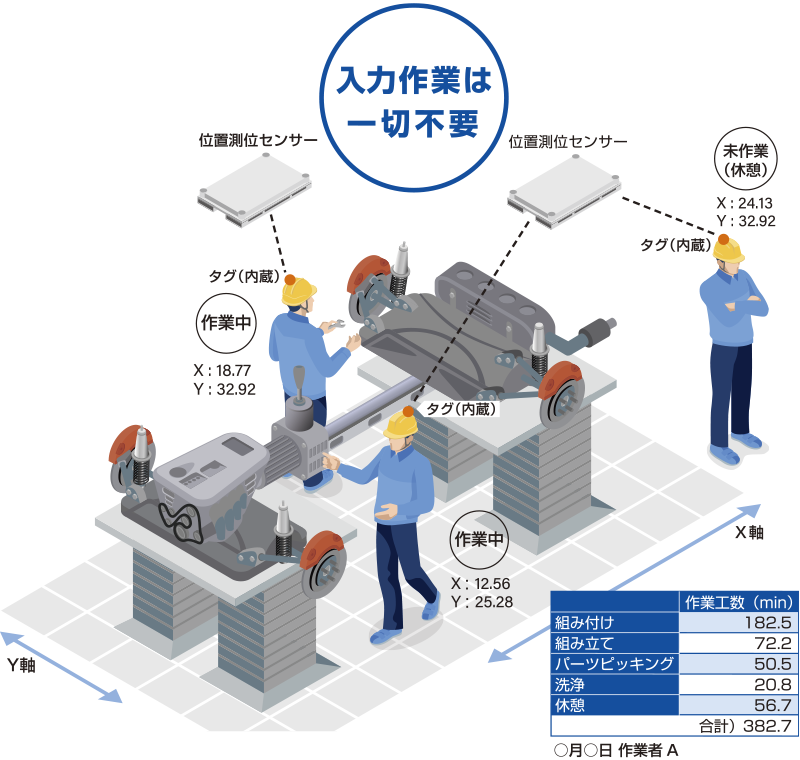
こちらの商品もご覧ください
当ソリューションに関するお問い合わせ
お客さまヘルプデスク24時間365日