新晃工業株式会社様
「作業の見える化が難しい現場で、エリア滞在率を数値化できたことが、改善に向けた大きな一歩となりました。」
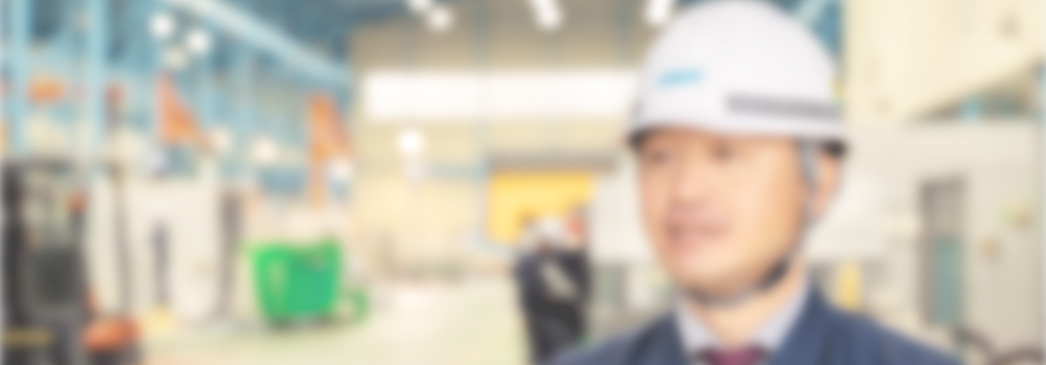
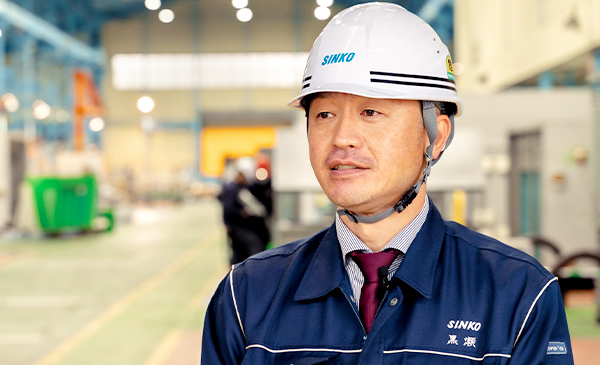
新晃工業株式会社
黒瀬 崇 様
生産本部
製造統括部 第一部長
導入経緯
業務用空調機器のトップメーカーである新晃工業株式会社様。商業施設やオフィスビル、病院、工場など、それぞれの環境に求められる「最適な空気」を作るための空調機器を設計・製造しています。
2007年からトヨタ生産方式を取り入れ、生産工程の改善に取り組んできましたが、作業者の作業状況の可視化ができておらず、生産性を上げるための打ち手が見つからない状況でした。
Before
作業者が持ち場で作業している時間を正確に把握できない
After
作業動線の可視化で、作業エリア滞在率が65%と判明
Before
生産性を上げるための改善策が見つからない
After
レイアウト変更や動線改善により作業エリア滞在率が86%に向上
Before
作業者のスキルアップが進まず効率的な生産体制が組めない
After
作業者のスキルアップができ柔軟性のある人員配置が可能に
導入システム
屋内位置測位技術を活用した作業可視化システム
- Ubisense RTLS(UWBリアルタイム位置測位システム)
- RaFLOW®(3D仮想マップ+動線分析ソフトウェア)
タグとUWBセンサーで作業者の動線を可視化
アクティブタグを作業者のヘルメットに装着し、工場内に設置した3次元測位可能なUWBセンサーで電波をキャッチすることで、作業者ごと、時間帯ごとにどんな動きをしていたのかを切り出して見ることが可能です。動きの特徴、ムリ、ムダが無いか確認することができます。
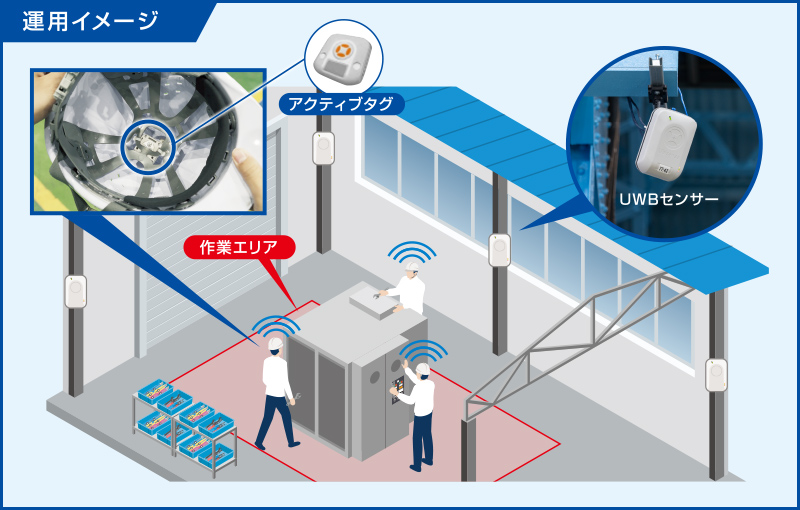
Before
工具置き場が作業エリアと離れていたために、作業者の動線に無駄があった
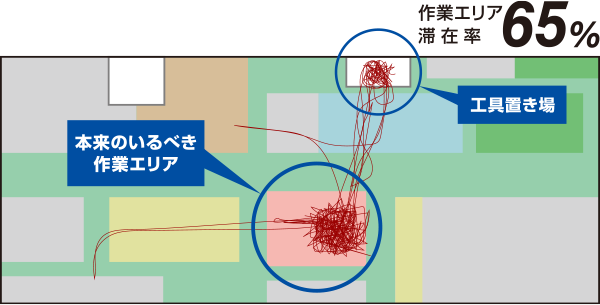
After
工具置き場の位置変更により動線に無駄がなくなり、作業エリア滞在率向上につながった
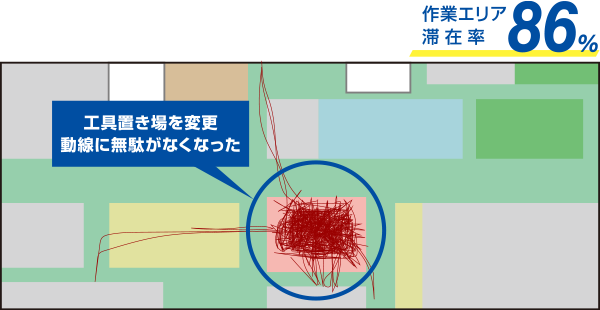
動画によるご紹介
お客さまの声
作業者が作業エリアから出てしまう! 作業状況の可視化が困難
当社では2007年からトヨタ生産方式を取り入れ、生産工程の改善に取り組んできました。その結果、仕掛品を減らすことには成功したのですが、作業者の作業エリア滞在時間、つまり付加価値を生み出すために費やす時間を増やすという取り組みはなかなか進みませんでした。「作業エリアから何回離れたか」「どこに何をしに行ったのか」をヒアリングしたり、記録を付けてもらったりしましたが、その申告は本当に正しいのか、実態を正確に把握することはできませんでした。
さまざまな対策を立て実践しましたが、成果につながっているのかもよく分からない。作業者の約9割が外国人なので言葉の壁もあり、こちらの意図を正確に伝えるのも、彼らが何に困っているのかをくみ取るのも難しかったですね。
位置測位技術の導入で判明したエリア滞在率は、なんと65%!
2017年の組織改編に伴い、トップからデジタル化を徹底的に促進するという経営方針が出されたのを受け、工数の自動取得に取り組むことになりました。当時、サトーからさまざまなソリューションを提案してもらった中で、作業者の動きを見える化できる「位置測位技術」の導入を決断しました。
位置測位技術を活用した作業可視化システムを導入して一番の驚きは、作業エリア滞在率が65%だと判明したことです。80%くらいは滞在しているだろうと期待していたので、正直かなり衝撃的な数字でした。とはいえ、数値化できたことは大きな成果でした。
午前中のエリア滞在率と動線軌跡を確認
作業者へのヒアリングで、1カ月で滞在率を86%に改善
エリア滞在率を改善するために、まず午前中の3時間のエリア滞在率を午後一番に確認するようにして、滞在率85%以下の作業者がいたら、「持ち場を離れていたようだけど、それはなぜ?」といったヒアリングをしました。同時に、工場内の動線分析もしました。その結果、検査機器や工具を取りに行ったり、工具の順番待ちをしたりすることが作業エリアを離れる原因のひとつになっていることが分かりました。そこで、工具の置き場所を変更したり、監督者が取りに行くことにしたり、また、「前工程から供給される部材を取りに行っていた」ことが分かった時は、部材の設置場所を変更するといった対応を取りました。このような改善を積み重ねた結果、エリア滞在率は1カ月で86%になりました。滞在率が低い原因を毎日確認して改善していく。その積み重ねが最も効果的でした。
正直、最初は、作業者の行動をモニターすることに対する反発もありました。無線タグを作業エリア内に置きっぱなしにした人もいましたね。そういった人に対しては、よりよい作業環境を作るために協力してほしいということを根気よく伝えました。持ち場を離れたことを責めるのではなく、エリア滞在率を上げるにはどうしたらいいかを作業者と一緒に考えることで、作業者の意識改革が一気に進みました。
さらなる効率化に向けて、部署を超えた多能化がスタート
エリア滞在率が改善したことで生産効率は明らかに向上しました。そこで、作業者の何名かには、前工程作業の教育を始めました。部署を超えた多能化です。一品一様なので、作業量が製品によって異なるため、部署を超えて応援ができる多能工を増やしたいという希望は前からあったのですが、位置測位技術導入の結果、教育に着手することができました。
今後はモノの動きも見える化したい。サトーの新しい技術に期待
今は、組み立て現場の“ヒト”の動きの見える化ができましたが、今後は、工場内の“モノ”の動きも見える化したいと考えています。例えば、フォークリフトや台車にセンサーを取り付けて工場内の運搬のムダを削減したり、仕掛品がどこにどれだけ滞留しているかなどを把握したりして、工場全体の改善点を洗い出したいです。
サトーは現場の課題をとてもよく理解してくれていますし、問い合わせをすればすぐに対応してくれます。15年のお付き合いになりますが、現場主義のサトーには信頼をおいています。
私たちが今後目指している、「さらなる自動化、省人化」につながる提案や新しい技術に期待しています。
お客さまプロフィール
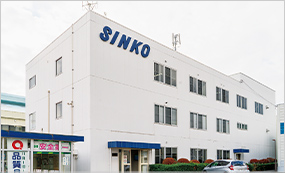
ご担当者様
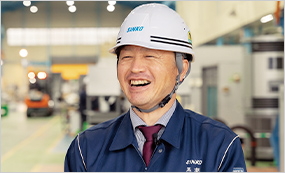
黒瀬 崇 様
関連リンク
導入事例に関するお問い合わせ
お客さまヘルプデスク24時間365日