TBロジスティクス株式会社様
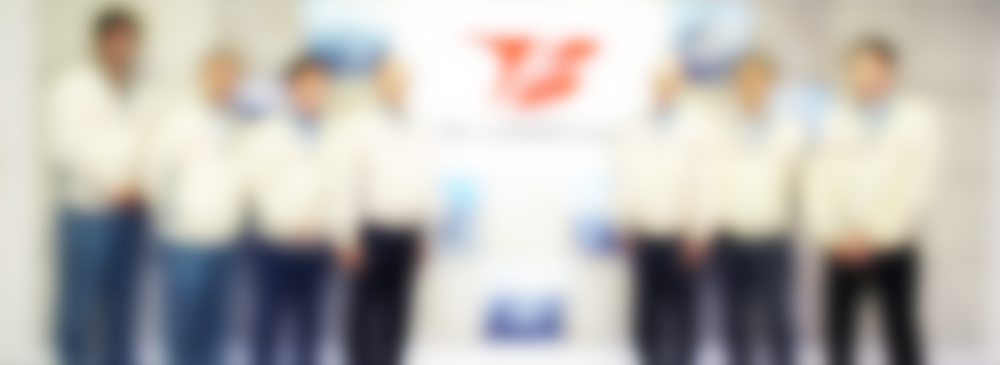
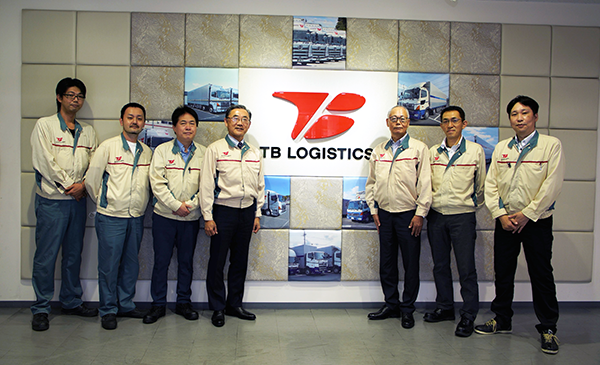
写真右から:物流・製造本部 生産・品質管理室 生産品質グループ 主任 倉増 正樹様 製造センター センター長 春田 英利様 取締役 柴田 賢治様 取締役社長 三輪 重孝様 製造センター 第2製造課 課長 竹内 常人様 製造センター 第1製造課 課長 江﨑 俊也様 物流センター第2製造課 シートカバー2係 工長 三浦 弘晃様
導入の経緯
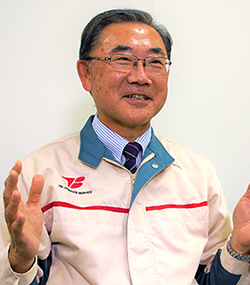
三輪氏
後工程であるお客さまに、間違った製品や不具合品を送らないということを、最大の目標にして取り組んでいます。ただ、現場には手作業で行っている業務があります。チェックシートを用いてミスが起こらないように配慮していますが、長く業務を続けていると“慣れ”が出てしまうことや、チェックシートにチェックをすることが目的となってしまい、肝心なチェックの部分が疎かになってしまうケースが稀にありました。
間違った製品や不具合品を後工程に送らない、この目標を達成すべく、RFID照合システムと音声検品システムを導入しました。
RFID照合システム・音声検品システム活用効果
- 目視によるピッキング、格納作業による照合ミス防止
- 出荷の際、順建て確認のため2人1組で読み上げ、チェック作業の改善
- 作業者の習熟にかかる期間の短縮
Before
- ①目視による格納・ピッキング作業を行っていたため、誤出荷が年間4、5件発生していた
- ②ピッキング業務の習熟にOJTを行い2週間かかる
- ③出荷の際、順建て確認のため2人1組で読み上げを行っていた
After
- ①RFID照合システムを導入後、誤出荷が0件になった
- ②業務の習熟が3日に短縮
- ③出荷時の確認作業が2人から1人に削減
動画によるご紹介
RFID照合システム
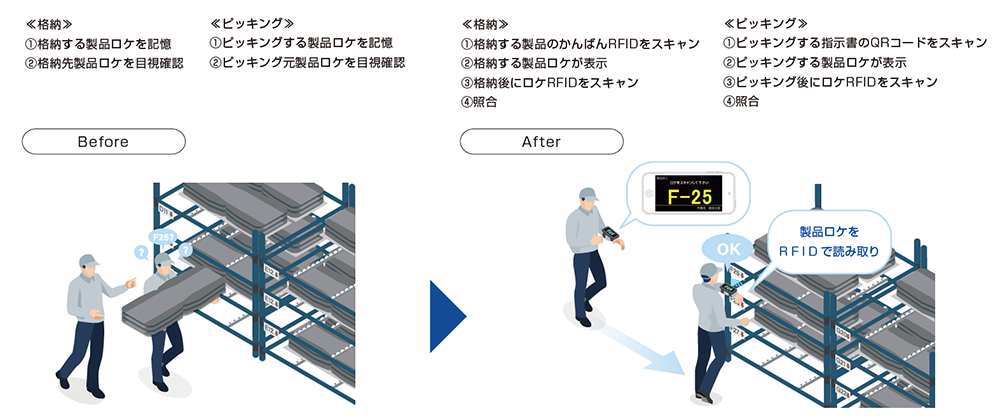
音声検品システム
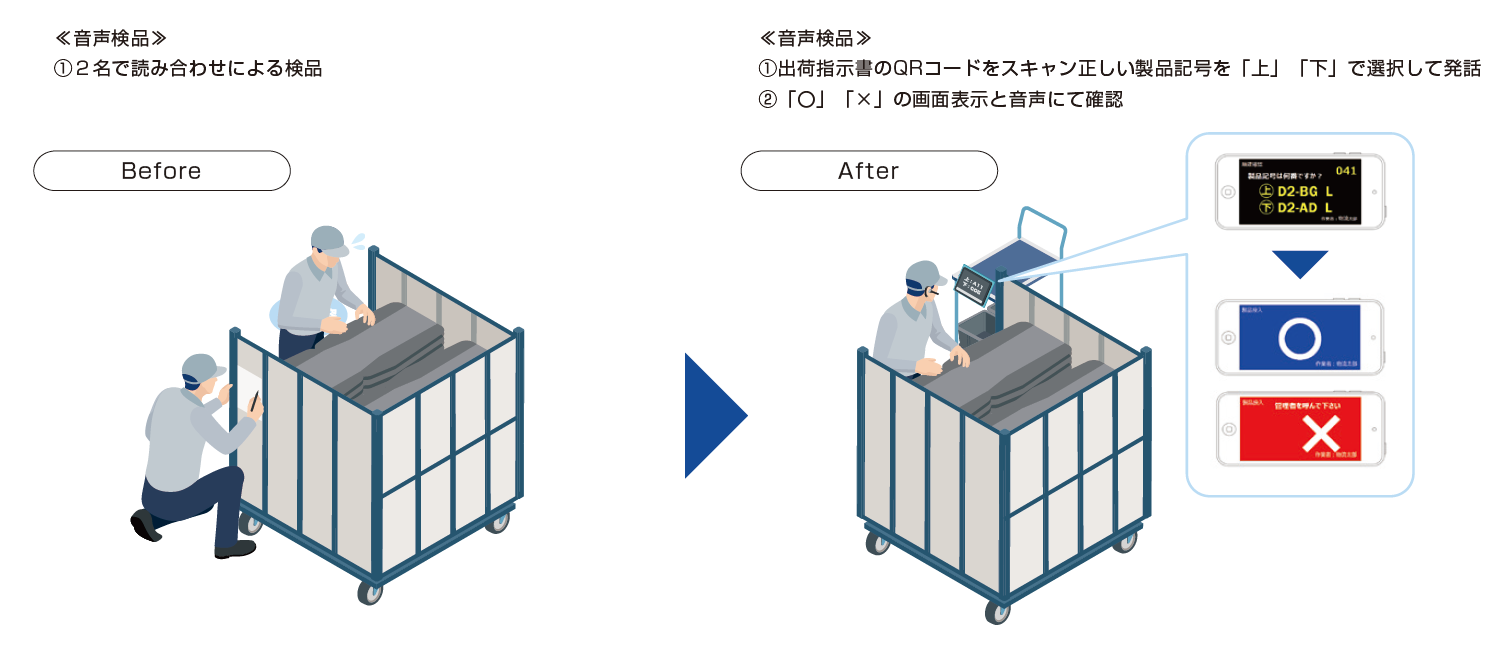
導入システム
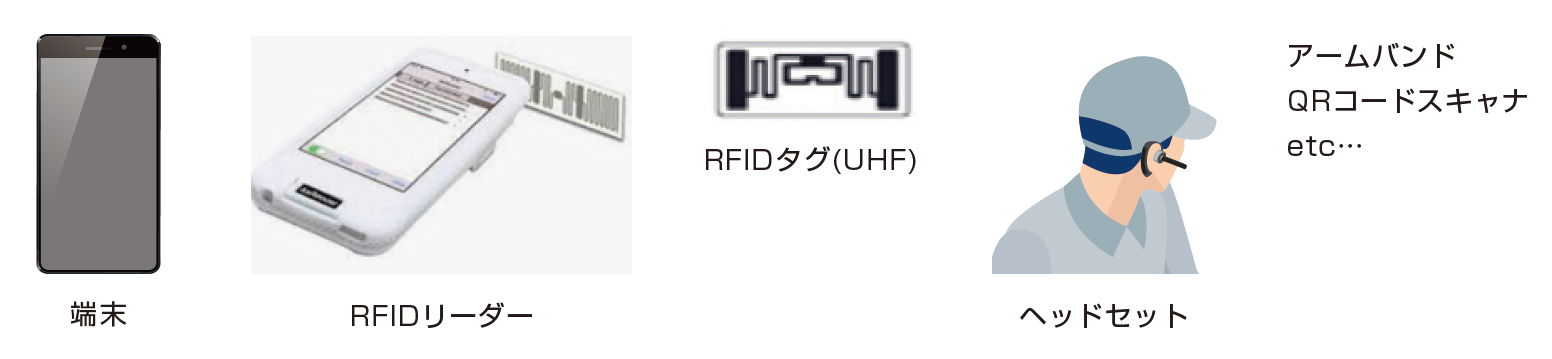
お客さまの声
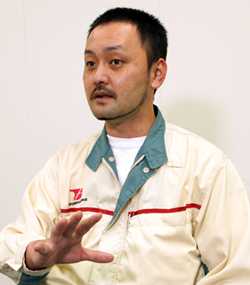
目視で照合を行っていたため誤出荷が4、5件発生していた
江崎氏
以前は製品を格納・ピッキング作業する際に照合できるツールがなかったので、RFID照合システムを導入するまではどうしても人の目に頼って作業を行っていました。
その結果、客先に対して年間4、5件の誤出荷が出ており、後工程にも迷惑をかけてしまっていました。それを何とかしなくてはと思っていたところに、サトー(さん)から今回導入したRFID照合システムと音声検品システムを提案していただきました。
RFID照合システムで習熟期間を短縮
江崎氏
これまでは製品の保管場所を記憶しなければならないので、作業の習熟に2週間ほどかかっていました。弊社では製品の保管場所を“製品ロケ”と呼んでいます。まずは製品ロケを覚えるところから始まるのですが、これに1、2週間ほどかかります。その期間は熟練工がOJTとして一緒に作業することになり、人員が割かれます。
RFID照合システムを導入してからは、製品ロケを覚える必要がなくなりました。システムの使用方法を覚える必要はありますが、3日もあれば覚えられるので、習熟期間を大幅に短縮できました。
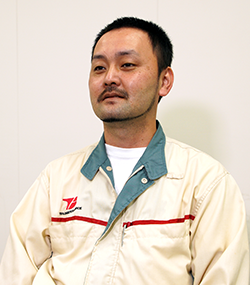
苦労した点
江崎氏
苦労した点は、RFID照合システムを導入する際にサイズ違いのタグを10種類用意してもらい、そこから弊社の運用に合うものを選定しました。製品ロケを取り付けている棚がイレクターパイプという金属でできているので、金属に強いRFIDを提案いただいたり、パイプからの距離、RFIDの大きさなど、さまざまな調整を行いました。苦労はしましたが、サトー(さん)と連携して電波強度の調整など試行錯誤を繰り返し、無事導入までたどり着きました。
システム導入前の不安点と導入後について
江崎氏
今まで使用していなかったシステムを導入することによって現場の作業者の負荷が増えないかという不安と、導入後に本当に役に立つ仕組みとして稼働するのかという懸念点がありました。システム導入の一番の目的である『誤出荷を出さない』点は、結果的に年間4、5件あった不具合が0件になり、お客さまにご迷惑をおかけすることもなくなりました。現場としても導入してよかったと思っています。業務的な視点でいえば、製品ロケを記憶しなくても作業ができることになり、作業者全員から高評価を受けています。
音声検品システムも同様で、1人でも、両手を使い作業ができるようになってとても助かっています。どちらも共通していえることは、作業者の「間違えていない」という安心感を得られたことは大きな成果だったと考えています。また、現場内のレイアウト変更が楽になったことも成果として挙げられます。今までは物が多く、作業スペースに入りきらないこともありましたが、レイアウト変更が容易にできることでそのようなことがなくなりました。整理整頓にもつながり導線の改善になっています。また、製品ロケに格納する際の入れ間違いが減ったことで、月に1度の棚卸しの時間も大幅に削減できています。
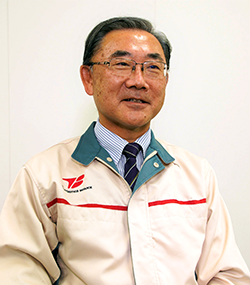
今後展望について
江崎氏
今後としては、弊社で導入したシステムを関連会社や業務委託先でも使用できないかという横展開を考えています。今後もサトー(さん)と連携しながら、業務改善ができそうな部分はシステム化を検討していきたいと思って期待しています。
三輪氏
日本国内での自動車生産台数が、これから右肩あがりになっていくということは望めないと考えています。そうなると、弊社の業務は将来的に海外とのやり取りがメインとなってくることが想定されます。
昨年10月に海外営業室を新体制でスタートさせました。今後は親会社からのアウトソーシングやエリア拡大など、海外物流に軸足を置いて進めていく予定です。海外事業を拡大していく上で、そこでもRFIDを活用していきたいと思います。
作業時間を削減したことで環境にも優しく

注意事項
CO2排出削減貢献量につきましては、総労働時間の変化と産業ごとの係数を基に算出した推計値です。実際のCO2削減量を保証するものではございません。
産業ごとの時間あたりCO2排出量係数(原単位)は、2021年3月時点の政府統計情報を基に作成しています。
お客さまプロフィール
関連リンク
導入事例に関するお問い合わせ
お客さまヘルプデスク24時間365日